项目名称:纳米材料气凝胶的非超临界产业化制备技术
牵头单位:弘大科技(北京)股份公司
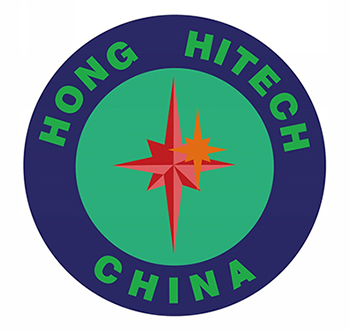
弘大科技(北京)股份公司成立于2013年12月,专注于新材料、新能源、节能环保等战略新兴材料研发、生产及销售的高新技术企业,总部位于中关村海淀园。公司全体同仁在“中关村高端领军人才”李光武董事长的带领下,独立自主研发,在全球最具潜力十大新材料中已成功突破三项:气凝胶非超临界产业化制备、非晶金属块材制备、创新了微晶纳孔金属。同时,在研发新能源蓄能、雾霾治理、生物灭菌、土壤改良、半导体基片制备等技术方面,均有领先世界的重大创新突破,已申请和获得专利40余项,气凝胶应用技术相关发明专利已有10余项。弘大科技,一个为世界科技进步做出贡献的中国企业。
参赛项目简介
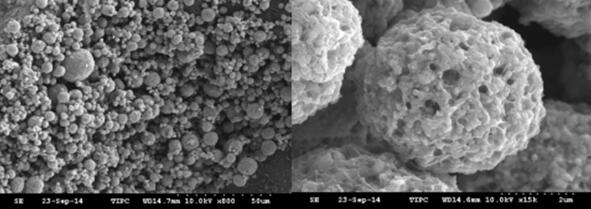
气凝胶,世界上最轻的固体、导热系数最低的材料,SCIENCE将气凝胶列为全球最具潜力十大新材料之一。气凝胶在热学、光学、电学、力学、声学等领域显示了许多奇特的性能,创下15 项吉尼斯纪录,被称之为“一个可以改变世界的神奇材料”,是具有巨大应用价值的军民两用技术,无论美国航天飞机还是战斗机都已经使用气凝胶用于隐形和防护。全球气凝胶最大生产厂家阿斯彭隶属于美国宇航局,因价格昂贵其产品主要在航天军工应用。
“气凝胶低成本产业化工艺技术和成套生产线项目”是李光武董事长带领研发团队历时近5年时间独立自主设计研发、突破关键核心技术、全过程实现国产化的原创性成果。该成果打破了国外专利封锁,批量产出的“神奇材料”气凝胶技术指标远超美国,已处于世界领先地位,且设备投资仅为世界普遍采用超临界干燥法的二十分之一。该项中国自主知识产权已获得国家发明和实用新型专利各1项,同时制备方法专利已获得中国、美国、日本、韩国、欧盟授权。
基于气凝胶的诸多优良特性,我公司持续研发了针对气凝胶应用的世界领先应用工程技术几十项,已申请发明专利31项,其中16项已授权、已授权实用新型专利15项。
气凝胶作为基础材料,应用范围极其广泛。将为我国节能环保、绿色建筑、国防军工、智能制造、集成电路、轨道交通、新能源、石油化工、新能源汽车等领域快速发展,做出举足轻重的贡献。目前,1万立方米气凝胶本体材料国内最大的生产基地已落户河南许昌,占全球产能的六分之一左右。气凝胶应用技术生产基地也即将落地,这两大基地的建成和运营将解决国家投入巨额资金研发近30年未能实现产业化的问题。
弘大科技核心产品有:气凝胶颗粒和粉末、气凝胶绝热毡、气凝胶防火保温板、气凝胶保暖纤维-弘暖纤、微晶纳孔金属、气凝胶超疏水涂料、气凝胶防火隔热涂料、气凝胶相变蓄能材料、气凝胶玻璃、气凝胶高能物理电容器电池、气凝胶用于汽车尾气排放净化装置。弘大科技在气凝胶产业化基础上,联合中科院化学所、理化所、北京有色金属研究院、北京工业大学、北京服装学院、燕山大学等科研院所的专家共同合作,申请了10余项的气凝胶应用技术相关发明专利。在气凝胶应用技术上取得了重大突破:如:1微晶纳孔铜基复合材料,该材料具有高强、高导电、高导热性能,再结晶温度较高,耐热性较好,能于400℃以下工作,在适当的热处理条件下,其硬度几乎是纯铜的3 倍,导电率可以达到95%IACS以上,导热率在401-438W/m.k,同时熔炼铸造成型方式可以突破高端铜合金制备设备及工艺限制,在产品性能、制备成本与制备工艺方面具有明显优势。主要应用领域是电子信息产业集成电路引线框架,国防军工用电子对抗、雷达、大功率军用微波管,高脉冲磁场导体,核装备和运载火箭、电磁弹射轨道、大破孔先进药型罩,高速轨道交通用架空导线等。2气凝胶防腐蚀涂料,该涂料拥有极其优异的超疏水、自清洁效果;对大部分基材都可以使用,比传统的疏水涂料性能更加优异且更加耐磨,使用寿命更长。3弘暖纤超级绝热保温纤维,该纤维具有良好的绝热保温性能,保温效果与现有产品比较,提高了5倍。每一个创新点都可带来相关材料产业的升级换代,从气凝胶的视角,将引领众多领域的划时代的变革。
公司荣誉:国家高新技术企业,北京市新技术新产品证书气凝胶
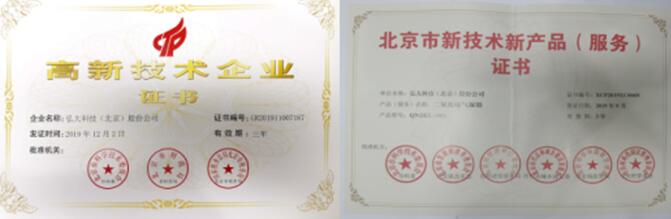
公司专利:
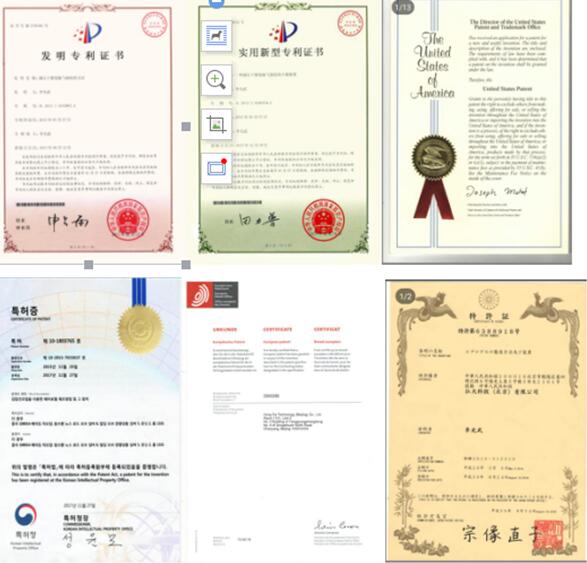
高价值专利培育情况
采用梯度减压技术制备气凝胶的设计思路:在2012年当时,全世界科学家虽然进行了几十年不断研究努力,基本制备思路持续停留在三种方法上,之一,最典型的超临界干燥制备气凝胶的技术,该技术从技术原理上利用置换介质超临界态消除气液界面的方法,避免了制备气凝胶时纳米孔隙结构坍塌问题,因此所有采用超临界态介质干燥制备气凝胶都会掉入已有专利中;之二,采用冷冻干燥技术制备气凝胶,既先将制备出的凝胶冷冻,再采用溶剂升华的方法逐渐去除各种溶剂及其液体,直至得到气凝胶,该方法已经有大量文献报道,且制备出气凝胶时间周期长、工艺设备复杂,且制备出的气凝胶品质不佳,即使设计出不同路径方法,形成专利也不具有价值;之三,采用常温常压技术制备气凝胶,由于气凝胶干燥时的坍塌现象是由于在气液固三相界面形成的向内坍塌力造成的,液体介质表面能越高,则坍塌力越大,这一技术采用的思路是采用低表面能溶剂置换制备凝胶时所采用的高或较高表面能溶剂和液体,使得干燥时塌陷力降到尽量低,但是,无论如何都会有的溶剂表面能只会使坍塌缓解而不会消除,所以得到的气凝胶品质不佳且效率不高。我们的穿心思路,首先摒弃掉传统的上述三种技术方案,同时要有基本技术原理支撑,还要具有更高生产效率,同时生产出更高品质产品。我们从干燥原理的设计考虑,既然干燥时所出现的是向内坍塌力,如果能够有一个想外的力平衡住,就可以避免向内坍塌;思想一下可以考虑到的方法有两个,其一,加热形成向外扩散气体,溶剂随着加热过程饱和蒸汽压就会增大,控制温度就可以控制压力,如果精准控制压力使溶剂向外扩散压力与向内坍塌力平衡,则可以逐渐加热得到干燥气凝胶;但是,通常的加热方法是由外到内的,外部温度高于内部就使得外部溶剂气体压力大于内部形成的气体压力,内部形成的气体很难向外扩散,而温度过高内部压力大于凝胶稳定承受压力时,凝胶破碎干燥得到的是没有纳米空隙的粉体;如果采用微波干燥,微波干燥原理是利用极性分子分子振动形成热效应,基本认为由内向外加热,但这种加热方式通常载波的中心温度更高,温度几乎不可控,又由于制备气凝胶的凝胶本身强度很低,内部溶剂形成的气体压力大于凝胶承受力时,凝胶破碎,只能得到没有纳米空隙的粉体。所以加热方式不可行。其二,就是我们所采用并得到授权的梯度减压干燥方式。既然在凝胶干燥制备气凝胶的过程中,凝胶的坍塌现象是由于在气液固三相界面形成的向内坍塌力造成的,如果在凝胶外部形成环境压力低于凝胶内部的情况时,其负压压力又与向内坍塌力平衡时,就可以避免凝胶的坍塌;实施的方法,就是首先将制备的凝胶置于密闭容器内,此容器带有排气管路,管路连接于真空泵上,这时,根据研究实验,设定初始负压压力,使得此压力既不破坏凝胶又可以将凝胶内部溶剂或液体所形成的饱和蒸气压所释放的气体排出密闭容器,则凝胶表面就会干燥形成一层带有纳米空袭的固体壳体,由于有了这一层固体壳体做支撑,带外部壳体的凝胶所能承受的向外溢出气体压力就会增大,同时负压抽出带壳体凝胶的阻力也会由于通道边长而增大,因此,就可以进一步降低压力抽出更深一层的内部溶剂和液体形成的气体,这样往复循环,随便面干燥的深化,合理降低压力,直至将内部溶剂和液体完全抽出并排除密闭容器。根据溶剂和液体蒸气压随温度升高而升高的特点,实际实施过程中可以给予凝胶一定温度,使得溶剂和液体气化更快,达到更高生产效率。